The Process and Applications of Plastic Gears
2023-10-20Mould & Die
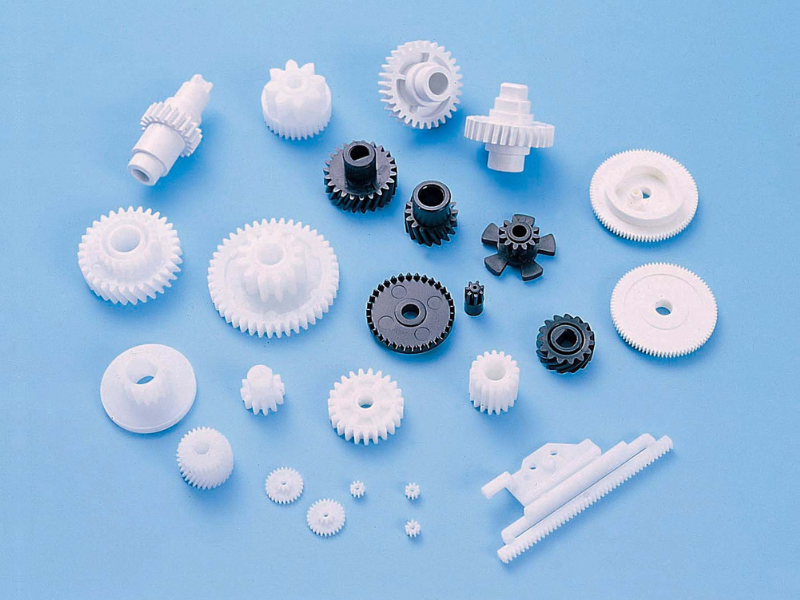
As a leading manufacturer of precision molds and plastic components in Taichung, Taiwan, MING-LI PRECISION STEEL MOLDS CO., LTD. is at the forefront of innovative manufacturing processes. One such crucial application is the production of plastic gears, which have become increasingly popular due to their versatility and performance characteristics. In this article, we will delve into the process of manufacturing plastic gears, explore their benefits, and highlight the wide range of applications they serve in various industries.
The Manufacturing Process of Plastic Gears
Plastic gears, though lightweight, can offer impressive mechanical properties and are often chosen over their metal counterparts for specific applications. The manufacturing process of plastic gears involves several stages:
- Material Selection: Choosing the right thermoplastic material is critical to ensure the gear's performance. Factors like load-bearing capacity, wear resistance, temperature range, and compatibility with the intended application need to be considered. Common materials used for plastic gears include nylon (PA), acetal (POM), polyethylene (PE), and polypropylene (PP).
- Gear Design: MING-LI's team of skilled engineers works closely with clients to design gears that meet their specific requirements. They take into account factors such as gear ratio, tooth profile, pitch, and the overall mechanical properties necessary for the gear to function effectively.
- Injection Molding: Injection molding is the primary method used for manufacturing plastic gears. In this process, the selected thermoplastic material is heated and injected into a precisely designed mold cavity under high pressure. The mold is typically made from steel and contains the inverse shape of the desired gear. Once injected, the molten plastic cools and solidifies inside the mold.
- Gear Finishing: After the gears are ejected from the molds, they undergo post-processing to achieve the desired finish. This may include deburring, trimming, and other surface treatment processes to enhance the gear's performance.
- Quality Control: MING-LI PRECISION STEEL MOLDS CO., LTD. employs stringent quality control measures to ensure that each plastic gear meets the required standards and specifications. This includes rigorous testing for dimensional accuracy, durability, and overall performance.
Advantages of Plastic Gears
Plastic gears offer several advantages that make them an attractive choice for various applications:
- Lightweight: Plastic gears are significantly lighter than metal gears, making them ideal for applications where weight reduction is crucial.
- Low Noise and Vibration: Plastic gears operate more quietly and generate less vibration compared to metal gears, making them suitable for noise-sensitive environments.
- Self-Lubricating: Certain plastic materials possess inherent self-lubricating properties, reducing the need for additional lubrication and maintenance.
- Corrosion Resistance: Plastic gears are resistant to corrosion, making them suitable for applications in challenging environments, such as marine and outdoor settings.
- Cost-Effective: The injection molding process used to manufacture plastic gears is cost-effective for high-volume production, making them a more affordable option compared to precision machined metal gears.
Applications of Plastic Gears
The versatility of plastic gears allows them to be used in various industries and applications, including:
- Automotive: Plastic gears find use in various automotive systems, including windshield wipers, window regulators, HVAC actuators, and electric power steering systems.
- Consumer Electronics: They are commonly used in electronic devices like printers, copiers, scanners, and digital cameras.
- Medical Devices: Plastic gears play a vital role in medical equipment such as infusion pumps, medical robots, and diagnostic devices.
- Home Appliances: They are found in appliances like washing machines, blenders, and coffee makers.
- Industrial Machinery: Plastic gears are used in various industrial machinery, such as conveyor systems, packaging equipment, and food processing machines.
- Toy Industry: Plastic gears are essential components in numerous toys, including remote-controlled cars and robots.
Customization and Engineering Expertise
MING-LI PRECISION STEEL MOLDS CO., LTD. prides itself on its ability to provide customized plastic gears tailored to meet the unique requirements of each client. The company's skilled engineering team collaborates closely with clients to understand their specific application needs and then designs and manufactures plastic gears with precision and reliability.
Conclusion
Plastic gears have emerged as a versatile and effective solution in various industries due to their lightweight, low noise, corrosion resistance, and cost-effectiveness. MING-LI PRECISION STEEL MOLDS CO., LTD., as a leading manufacturer of precision molds and plastic components in Taichung, Taiwan, is at the forefront of delivering high-quality plastic gears for a wide range of applications. With their engineering expertise, commitment to innovation, and state-of-the-art injection molding technology, MING-LI continues to be a trusted partner for businesses seeking durable and efficient plastic gear solutions.