SA-Tools' Guide to Choosing the Perfect Ball Nose End Mill
2023-10-23Mould & Die
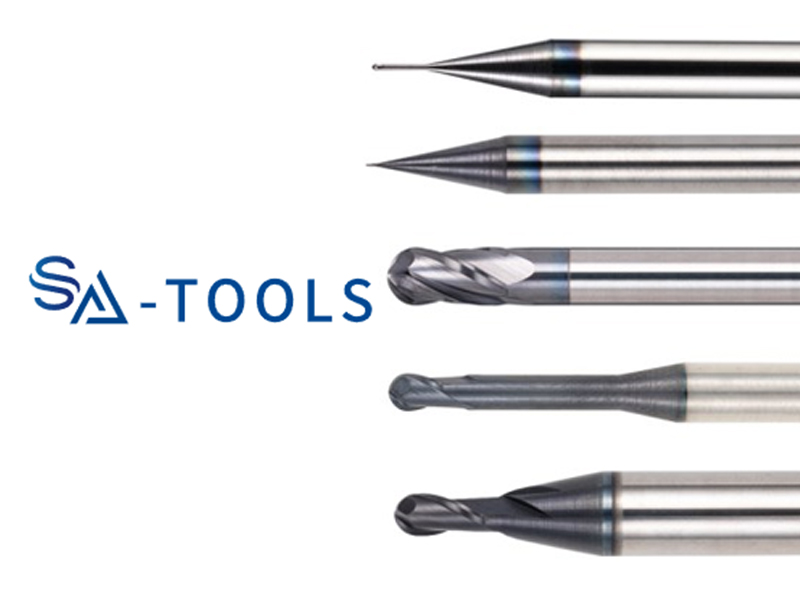
In the intricate world of precision machining, selecting the right tool can be the key to unlocking your full potential as a manufacturer. At SA-Tools, we understand the significance of choosing the perfect ball nose end mill. In this comprehensive guide, we build upon our previous article on ball nose end mills (which you can find here), to provide you with a step-by-step guideline for purchasing the ideal ball nose end mill for your machining needs.
Step 1: Understand Your Material (As mentioned in our previous article)
Just as a painter selects different brushes for various canvases, machinists must consider the material they're working with. Hard materials like hardened steel demand a different tool compared to softer materials like plastic or wood. SA-Tools offers a wide range of ball nose end mills, each tailored to specific materials.
Step 2: Determine the Geometry (As mentioned in our previous article)
Consider the complexity of your project. For intricate 3D contours, a ball nose end mill is invaluable. The spherical tip allows for smooth and precise machining on curved surfaces, just as an artist's brush can smoothly stroke the canvas.
Step 3: Choose the Right Coating (As mentioned in our previous article)
Coatings can greatly influence tool performance. SA-Tools' ball nose end mills come with various coatings, each offering unique advantages. For instance, TiN (Titanium Nitride) or TiAlN (Titanium Aluminum Nitride) coatings provide enhanced wear resistance, prolonging tool life.
Step 4: Consider Flute Count and Helix Angle
The number of flutes on a ball nose end mill can impact performance. More flutes can result in a better surface finish but may reduce chip evacuation efficiency. Fewer flutes can be more effective for roughing but might leave a less refined surface. The helix angle also influences chip evacuation and tool stability.
Step 5: Review Cutting Parameters
Don't forget to adjust cutting parameters such as cutting speed, feed rate, and depth of cut. These factors can significantly affect the performance of your ball nose end mill. SA-Tools can provide guidance on the ideal parameters for your specific tool and material.
Step 6: Plan Your Toolpaths Carefully
Just as an artist plans their brushstrokes, meticulous toolpath planning is crucial. This is especially important for 3D contouring with a ball nose end mill. Carefully consider the toolpath strategy to minimize tool engagement and reduce the risk of tool breakage.
Step 7: Inspect and Maintain Your Tools
Regularly inspect your ball nose end mills for wear and damage. Replace them when necessary to ensure consistent and precise machining. SA-Tools takes pride in offering durable and reliable tools, but maintenance is still essential for optimal performance.
Step 8: Consult SA-Tools' Experts
Choosing the right ball nose end mill can be a complex task. If you're uncertain about which tool is best suited for your project, don't hesitate to reach out to SA-Tools' experts. We have a team of knowledgeable professionals ready to provide guidance and recommendations tailored to your specific machining needs.
In conclusion, selecting the perfect ball nose end mill is a crucial step in achieving precision and efficiency in your machining endeavors. With SA-Tools' wide range of options and our expertise at your disposal, you can embark on your machining projects with confidence, knowing that you have the right tool for the job.