Wire EDM Parts
2022-06-06Mould & Die From:OSCAR E.D.M. COMPANY LTD.
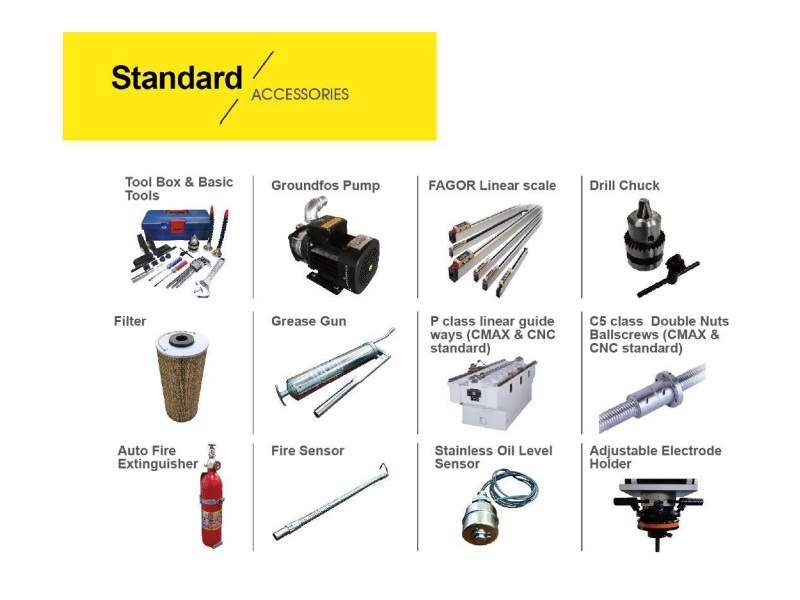
The wire electrical discharge machining process is mostly used to create complicated forms and patterns in hard metals. Normally, they are tough to shape, mold, or manipulate. The system is the culmination of the assembly of intricately designed components.
Electrical Discharge Machining is classified into two broad categories: ram EDM and Wire EDM. We shall examine just the latter - wire EDM - in this text.
What is wire electrical discharge machining, or Wire EDM?
Wire EDM is a process that enables hard metals that were previously incapable of being machined or manipulated by conventional methods to be machined, manipulated, and designed using electrical charges to cut away the unwanted metal and create previously unattainable shapes and designs with greater tolerances and precision.
One constraint on wire EDM is that the material used must be electrically conductive. A typical machining technique is to mount a metal pipe on a lathe and turn it while cutting it with a carbide tip or any comparable cutting tool; this is similar to how wood is lathe-cut. While this is a very simple example that demonstrates the huge range of possible variations between products, Wire EDM enables firms to now make considerably more sophisticated goods from metals that were previously unworkable, including cutting forms into 3D and incredibly intricate Jewelry patterns.
Wire EDM Components
The chiller is a critical component of wire electrical discharge machining and plays a critical role in operation, since it regulates the system's temperature. Flushing is critical for the wire electrode to move freely when cutting a piece, and the flush cups provide a smooth procedure.
Without the EDM wires, wire electrical discharge machining makes no sense. These cables form the system's foundation. They operate as electrodes, isolating the conductive portion from the substance. EDM wires come in a variety of grades. Each has a unique coating and has been time-improved for improved cutting. Zinc, copper, tungsten, and brass EDM wires are available. EDM wires come in a variety of diameters for customized cutting. A narrower wire produces a more restricted slit or space than a thicker wire. Numerous manufacturers now use high-performance brass wires that are alloyed with a higher amount of zinc, allowing for quicker and more precise cutting.
The patterns are created on the CNC system using a computer. It has been enhanced with software that permits precise cutting. Advanced software, such as CAD and CAM, is used to program the CNC equipment. Additionally, the power-feed connections are critical and are built entirely of tungsten.
Filtration is another critical procedure in the wire electrical discharge machining process. It contributes to cost savings in operation. Numerous filter systems are available with a variety of filter cartridges, which all contribute to the overall efficiency. Wire electrical discharge machining is a versatile process that meets the different demands of the industrial industry.